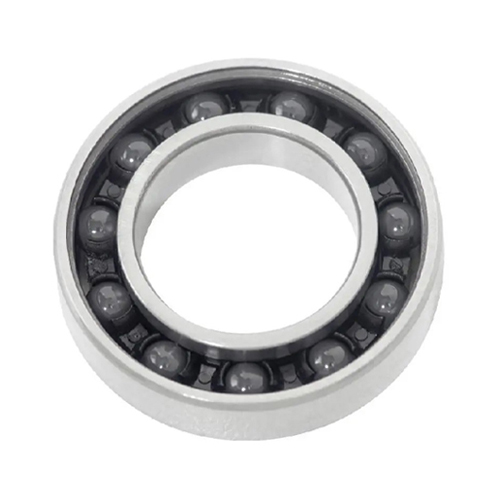
In the development and application of engineering ceramic products, ceramic ball bearings are typical examples of engineering ceramics in the industrial field, and have been highly valued by many countries. Among the high-speed precision bearings, the most widely used is the hybrid ceramic ball bearing, that is, the rolling element uses the hot-pressed Si3N4 ceramic ball, and the bearing ring is still a steel ring. This kind of bearing has a high degree of standardization, small changes to the machine structure, easy maintenance, and is especially suitable for high-speed operation. The assembled high-speed electric spindle has the advantages of high speed, high rigidity, high power and long life. 1. Bearing configuration: inner and outer ring bearing steel / stainless steel + ceramic ball + PA66 / stainless steel retainer +2RS / ZZ2. high temperature grease, 3. the advantages of using ceramic ball bearings and ordinary bearings
advantage
High temperature resistance
The thermal expansion coefficient of the ceramic ball is small. In the high temperature environment, the bearing ball will not expand due to the temperature, which greatly improves the use temperature of the whole bearing. The temperature of the ordinary bearing is about 160 degrees, and the ceramic ball can reach 220 degrees or more.
High speed
The ceramic ball has oil-free self-lubricating property, and the ceramic ball has a small friction coefficient, so the ceramic ball bearing has a high rotational speed. According to statistics, the bearing of the ceramic ball is the rotational speed of the general bearing of 1.5 times or more.
long life
The ceramic ball can be free of any grease, which means that even if the grease is dry, the bearing can still work, thus avoiding the premature bearing damage caused by the grease being dried in the ordinary bearing. According to our test and feedback from some customers. The service life of the bearing behind the ceramic ball is 2-3 times that of the ordinary bearing.
insulation
The last point is also the most important point. Insulation, ceramic ball bearings can be used to insulate the inner and outer rings of the bearing. Because the ceramic ball is an insulator, the ceramic ball can be used between the inner and outer rings of the bearing to achieve the insulation effect. This allows the bearing to be used in an electrically conductive environment. The rolling bearing consists of a ferrule, a rolling element, a retainer, a grease, and a seal. When the rolling element is made of a ceramic material, the rolling bearing is defined as a ceramic ball bearing.
composition
Because the ceramic ball itself has self-lubricating properties, the lubrication can be used according to the requirements of the application, and it can be either greased or not. The seal can also determine whether the ceramic ball bearing has a seal according to the requirements of use. The holder can also be used according to the requirements of use. Then the ferrule and the rolling element are two indispensable elements of the bearing. When these two elements are not the same material, there is a saying of Hybrid construction bearing. When the rolling element is made of a ceramic material, it is defined as a hybrid ceramic ball bearing. Commonly used ceramic ball materials are zirconia (ZRO2) and silicon nitride (SI3N4); commonly used ferrule materials are bearing steel (GCR15) and stainless steel (440, 440C) and stainless steel (304, 316, 316L).
According to the use environment, rotation speed, load, temperature, and requirements during use, the ferrule and rolling element of the ceramic ball bearing can be combined with each other and have different effects.
Ceramic ball bearing code:
HY + ferrule material + bearing type + seal type - ball material - retainer material - grease
Ferrule material: S means stainless steel SS means stainless steel What material can be specified by registered mark
Characteristics
Practice has proved that as a bearing material, it must also have dimensional stability at different temperatures to ensure that the bearing maintains precise dimensions and precise fit under temperature changing working conditions. In special circumstances, it must also have corrosion resistance and decomposition resistance. ability. In summary, ceramic materials used to make rolling bearing parts should have the following performance characteristics:
1) Low density. Due to the reduced density of the rolling elements, the centrifugal load is also reduced at high speeds, allowing operation at higher speeds.
2) Medium elastic modulus. If the modulus of elasticity is too large, the bearing capacity of the bushing will be reduced due to stress concentration.
3) The coefficient of thermal expansion is small. Reduce the sensitivity to temperature changes, making the bearing operating temperature range wider.
4) High compressive strength. High compressive strength is the need for rolling bearings to withstand high stresses.
5) High hardness and high toughness. The combination of these two characteristics can achieve better surface roughness; and it can prevent damage from external particles and impact.
6) Good resistance to rolling contact fatigue and flaking failure mode.
7) Special occasions should have high temperature resistance, corrosion resistance and stability.
The ferrule and the rolling element contact point are subjected to an applied load and rotation, thereby repeatedly generating contact pressure and deformation. Due to the material properties of steel bearings, the main form of bearing failure is fatigue spalling, short fatigue life, and the application range is greatly limited. The ceramic material has low density, medium elastic modulus, small thermal expansion coefficient, high hardness, high temperature resistance, corrosion resistance, no magnetism, etc. Ceramic ball bearings with silicon nitride ceramic balls as rolling elements can significantly improve bearing contact fatigue life. It has greatly expanded the application fields of rolling bearings and has been widely used in various high-precision, high-speed machine tools, automobiles, racing cars, subways, motors, aero engines, petrochemical machinery, metallurgical machinery and other fields.
Direction of development
Since the ceramic ball bearing is an important mechanical basic component, it has excellent performance unmatched by metal bearings, and therefore has been widely used in various fields. From the perspective of the application effect, the most prominent effect is to greatly improve the service life and limit speed of the bearing, providing basic components for the development of high-speed, high-precision machine tools. In addition, in high temperature, corrosion, insulation, vacuum and other industries have also achieved good results. Based on its wide range of applications, it has brought greater vitality and vitality to its development. In addition, developers should pay attention to the most common work that metal bearings are not capable of, and ceramic bearings are fully capable of replacing. Such as sewage treatment, marine development, oil exploration, medical and health, food industry and other fields in the general use of the accuracy level, medium and low speed, the bearing can be resistant to a certain concentration of acid, alkali, salt corrosion, resistance to several hundred high temperature , non-magnetic, electric, non-toxic, can be used in the field of work without oil or using the working medium itself to lubricate. The bearings used in these fields account for a large proportion of special bearing applications, and the market is vast and worthy of our development. R&D institutions should seize opportunities, open up markets, reduce manufacturing costs, promote large-scale production of high-performance ceramic materials, and enable the industrialization of ceramic materials with broad market prospects.