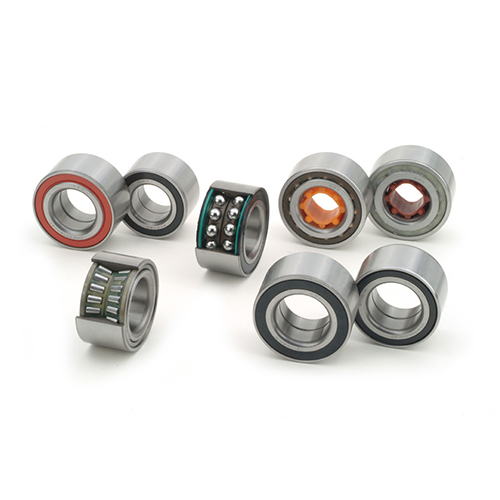
The hub bearing is one of the key components of the car. Its main function is to carry the weight and provide precise guidance for the rotation of the hub, which requires it to withstand both axial and radial loads.
The traditional automotive wheel bearings are composed of two sets of tapered roller bearings or ball bearings. The installation, oiling, sealing and clearance adjustment of the bearings are carried out on the automobile production line. This structure makes it difficult to assemble in a car production plant, high in cost, and poor in reliability, and the car needs to be cleaned, oiled, and adjusted at the time of maintenance at the maintenance point.
The hub bearing unit is developed on the basis of standard angular contact ball bearings and tapered roller bearings. It integrates two sets of bearings and has good assembly performance, can eliminate clearance adjustment, light weight, compact structure and load capacity. Large, sealed bearings can be pre-loaded with grease, omitting external hub seals and maintenance-free. They have been widely used in cars, and there is a tendency to gradually expand applications in trucks.
development path
The largest number of wheel bearings for cars used in the past was the use of single row tapered roller or ball bearings in pairs. With the development of technology, car hub units have been widely used in cars. The range and use of hub bearing units is growing, and has now reached the fourth generation:
The first generation consisted of double row angular contact bearings.
The second generation has a flange for fixing the bearing on the outer raceway, which can be simply fixed to the axle by a nut. Make the maintenance of the car easier.
The third-generation hub bearing unit is equipped with a bearing unit and an anti-lock brake system ABS. The hub unit is designed with an inner flange and an outer flange, the inner flange is bolted to the drive shaft, and the outer flange mounts the entire bearing together.
The fourth-generation hub bearing unit integrates the constant velocity joint with the bearing, which solves the disadvantages of the prior art that the weight of the hub is increased due to the integral structure of the hub and the constant velocity joint. The development of the fourth-generation wheel bearing unit has been successful, and it is believed that it will be widely used in various types of vehicles in the near future. The characteristics of these unit products are: no need to adjust the bearing assembly gap, the bearing assembly process is more reasonable, the weight is reduced and the volume is reduced, and it can be used almost permanently after one-time loading, which reduces the overall production cost and is more conducive to large-scale popularization.
Technology and development trends
High performance seal
Because the hub bearing is very close to the ground and high temperature brake discs and other parts, it needs to adapt to various complicated road conditions and harsh driving conditions. Therefore, the bearing seal must have good grease leakage resistance, and must also have good heat, mud and sewage resistance.
Shake technology
The third-generation wheel bearing generally adopts the self-locking semi-inner ring of the rocking technology. When the rocking technology is used, the axial load causes the spindle end of the wheel to be plastically deformed, so that the hub main shaft and the semi-inner ring are integrally connected. Compared to conventional nut tightening, third-generation hub bearings with rocking technology help reduce size and weight while reducing cost and improving the reliability of the hub bearings. At the same time, the step of adjusting the position of the internal components is eliminated when assembling to the car.
Lightweight miniaturization
The second-generation and third-generation wheel bearing structure design must be finite element analysis to ensure that the flange is sufficiently rigid while minimizing its volume and weight. The rigidity of the third-generation wheel bearing is the hub method. The angle of inclination of the flange relative to the flange of the outer ring. Through the integration and miniaturization design to reduce the weight of the axle, the second generation of hub bearings reduced 180g than the first generation, and the third generation of hub bearings further reduced the weight of 120g.
Low friction torque
The important measure to reduce the fuel consumption of the automobile is to design the hub bearing with low friction torque. The main factors affecting the friction torque of the bearing are the type of bearing and the preloading load. The bearing seal also accounts for a large proportion of the friction torque component. Therefore, improving the seal design and reducing the friction torque can significantly improve the performance of the hub bearing. The wheel bearing has been developed from the first generation to the latest fourth generation, and the friction torque is gradually reduced.
ABS technology
ABS is an automobile safety control device with the advantages of anti-skid and anti-locking. When the vehicle is in emergency braking, the brake speed is automatically adjusted to prevent the wheel from locking and shortening the braking distance. The detection of the rotational speed is carried out by a magnetic sensor mounted on the part that rotates with the wheel and fixed on the vehicle body in the vicinity. The hub unit with ABS sensor is divided into two cases: one is placed inside the hub, and the sensor is mounted on other parts; the other is placed inside the hub together with the sensor (called sensor hub unit).